The large diesel machines we have all grown to know and love, are changing with the introduction of new technologies. With sustainability and efficiency being pushed more than ever, our industry is starting to feel a for change with ecological effect and footprint in mind.
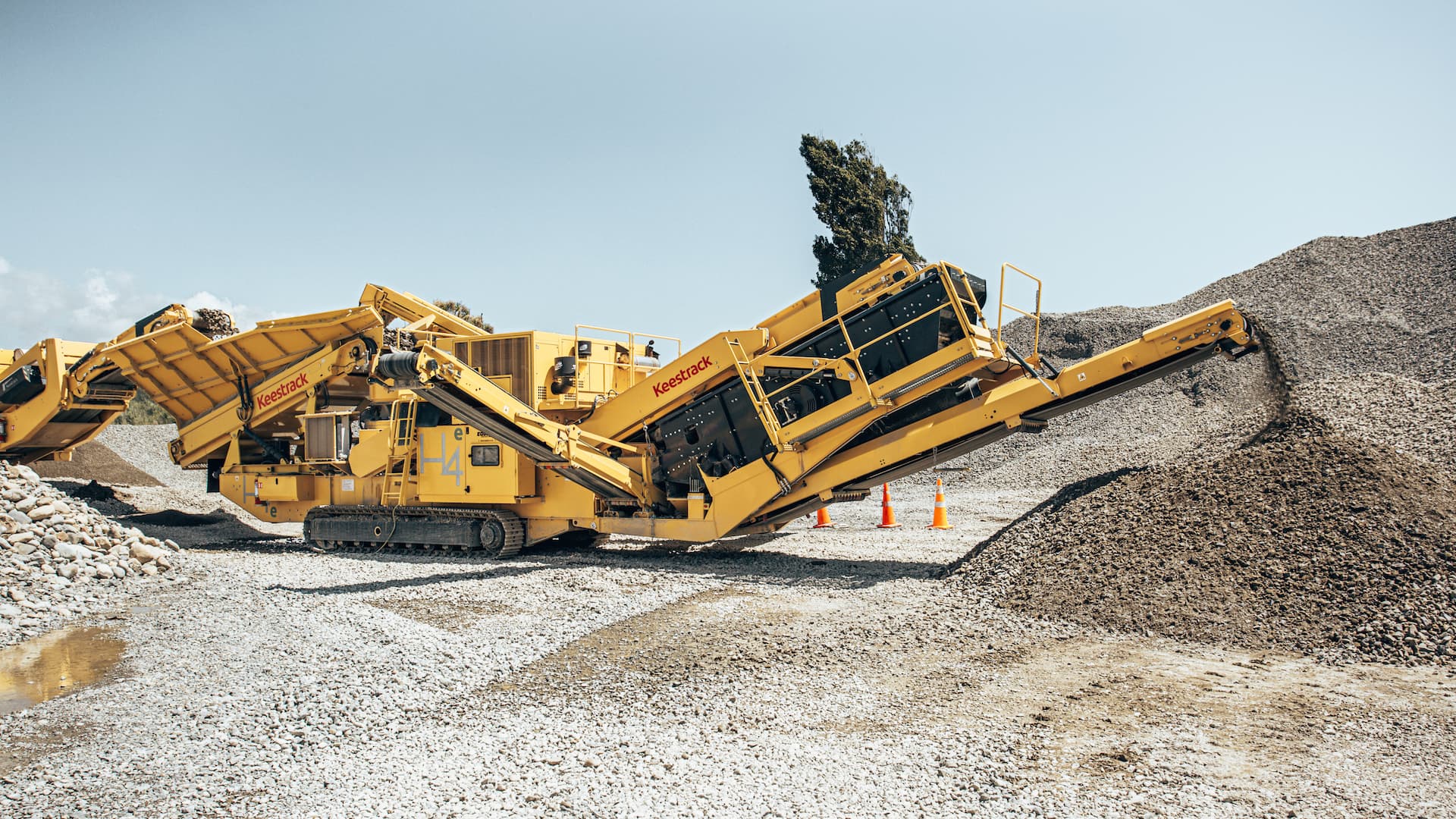
In the following article, we will be going over the possible savings created by electric tech, the basics of electric drive systems, and the differences between true electric and hydraulic electric, and why E-Machines make a great option for businesses looking to keep a high standard and volume of output while moving to a more sustainable (and cheaper) energy source. Before we look into the technical details, we’ll compare the important numbers, applied to business and electric vs diesel-hydraulic. We're all in business to make money; when the cost of producing something decreases, margins go up. So, if a machine was substantially more efficient for the same production volume, it would be logical to conclude it would positively affect your margin, with E-Machines it’s a 30% energy difference and thus cost-saving.
Keestrack and Equip2 have put time into research comparing a traditional diesel-hydraulic with a Keestrack diesel-hydraulic and Keestrack E series machines (optionally powered by their own diesel generator); the differences are substantial.
Below, we compare a Keestrack R3 (Diesel-Hydraulic with Load Sensing Pumps), Keestrack R3e (E Series Electric/Hybrid), and a close market competitor on their consumption, energy usage, initial outlay, and maintenance.
Diesel-Hydraulic vs Electric: The Numbers
First, we’ll compare the initial investment cost of the equipment. Although in its lifetime this cost is small, the E-Machine is slightly more costly initially. It’s important to note that the advantage is found in its lower running cost and longer maintenance intervals. As evidenced further on.
Of the three machines, the competitor and R3h cost about the same, with the R3e costing 3% more. The initial outlay is significant on any crusher; however, considering how much you could save in running costs, the 3% difference in price can be quickly negated.
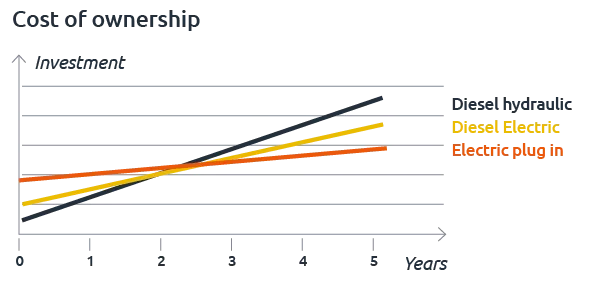
When comparing fuel consumption per hour, the efficiency differences start to become apparent. The R3h is more efficient than the competing machine, due to the load sensing pumps. The R3e can be powered by either its onboard gen-set or directly from the grid, both still offer substantial fuel savings.
1 Kilowatt/Hour (Kwh) costs around $0.1629, where 1 litre of diesel costs about $1.20.
Why does the R3h and R3e perform better? Energy efficiency. The R3h (Diesel-Hydraulic) uses load-sensing pumps that don’t draw hydraulic pressure when not needed, which reduces engine load and thus consumption, its standard operation is around 53% efficient. The R3e on the other hand uses electric motors which boast much higher efficiency as there are minimal pumping and distribution losses for the same power output, the R3e’s standard operation is around 82% efficient.
The above comparisons only go as far as to consider the running cost. When we start considering maintenance and everything else that goes along with running one of these machines for more than a few hours, the differences become even more evident. When looking at wear parts, the R3e is built on the proven R3 platform; all wear parts such as screens, blow bars, wear plates, and more are the same. Therefore the cost of maintaining these parts is pretty consistent on both the diesel and electric machines; however, the differences are in the maintenance of the drive system.
With a diesel machine, maintenance of the drive system includes regular oil changes, greasing of bearings, 500 and 1000 hour services, coolant, injectors, hydraulic fluid, filters, etc. Compared with electric machines (when run on the grid), whose maintenance of the drive system consists of regular greasing and inspections of the bearings and shaft, the time and cost of maintaining these machines are significantly less. The only situation in which these machines require similar maintenance is when the diesel gen-set is being used to power the machine. It is important to note that this machine is still a crusher, and the standard wear parts still need replacing.
However, when something does more work to achieve the same result, its life expectancy is usually shorter. This becomes apparent when looking at the life expectancy of the motors.
When we consider the end of the line product and how much it costs to make, not including the initial outset or maintenance, the figure mentioned earlier of a 30% difference is highlighted.
Decreasing production costs by a few cents per tonne will largely affect your bottom line. If 30% on every dollar of production cost was saved over the year, what would that add up to, and how quickly would that 14% difference in the initial price be covered? If you want to know if an E-Machine would work for you, Equip2 can produce a machine audit based on all the above costs for a direct in-quarry comparison.
How It Works
With the numbers out of the way, we can get into the nitty-gritty details.
For comparison's sake, we have three different types of crusher drive systems, diesel direct drive, hydraulic, and electric direct. For all intents and purposes, we will focus on the electric direct drives for this article. If you are interested in learning more about the different types of crusher drive systems, see our article "Crusher Drive Systems."
The bare basics of electric motors are simple: place an electromagnet within a circular magnetic field, and power it to cause rotation of the shaft. Now increase the scale substantially and you're looking at the bare bones of the Keestrack E-series direct drives. Without delving into dialogue on the types of crushers, the electric motors replace the hydraulic motors connected to the conveyor belts, screen boxes, and direct drive shafts of the different crushers.
Simpler Is Better
When you compare this drive to that of a diesel machine, the beautiful simplicity of electric becomes apparent. Electric motors like the type pictured above and in our machines only have one moving part: the shaft. If one was to use grid power, then the need to have regular diesel engine services may be negated. If one was to use only the equipped diesel generator, then there is no need to have hydraulic systems serviced. Not to say that the E-Machines don’t need servicing, they still do, however they won’t need hydraulic services or diesel engine services if the owner chooses to run the machine off the grid.
The distinction between diesel and electric is pretty straightforward, one is powered with fuel, and one is powered with electricity. However, this distinction may not be as easily made between fully electric machines and hydraulic-electric machines.
In this instance, one form of electric is a direct drive for the componentry, which does the crushing; the other uses an electric motor to create hydraulic pressure, which drives the crusher and various components.
Hydraulic-electric systems use an electric motor like in a direct electric drive. Where it differs is the way the power is used. The power from the electric motor within the hydraulic electric machine is delivered to a transfer and pump, which then generates hydraulic pressure that componentry can be plumbed off of. While this system has its advantages, specifically the ability to create a high amount of force, the pitfalls compared with direct electric are apparent; the machine is often more complicated with more moving parts. On top of the electric setup, there is a need for hydraulic plumbing, pressure assistance systems, and all the valves that go with it. Eventually, this adds more to the cost of operation, and, if something goes wrong, this system has the potential to cost more to fix. While this system has more efficiency than diesel systems, it is still not as simple and efficient as a direct electric system.
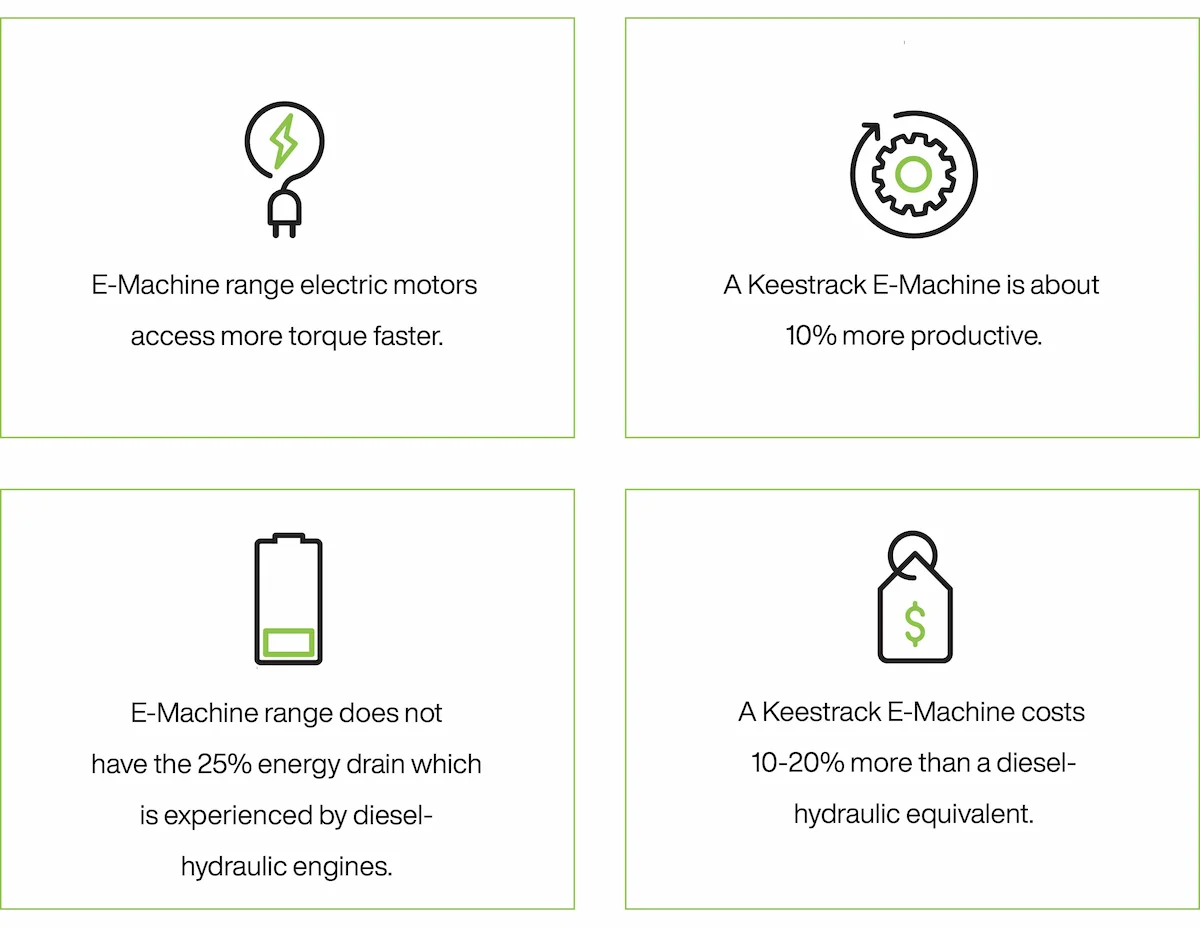
Your Choice
This brings us to the point of defining true electric. Here at Equip2, we want to stick to our core values of making things better and delivering the best. If you are looking to up your efficiency and take a much more sustainable approach in your work, why would you buy machinery which isn't going to lead its field in savings, and doesn’t truly deliver a sustainable result?
When we say electric technology, we mean just that; true electric to us, is the beautiful simplicity and efficiency of direct electric, and nothing more. Although we provided information on powering these machines with a generator, we didn’t elaborate and state that the generator is a standard fitting on all e-machines. These generators allow the Keestrack e-machines to self-power without the consumption of traditional diesel drives.
This is quite important because, for the time being, New Zealand still uses diesel as our primary energy source for large machinery, and we aren't getting away from it for a while. Machines like the H4e give you the ability to power your machine with diesel via the generator until you reach a point where you decide to swap over to running it on grid power. Even while running it via the generator, you still save up to 12% on your final product cost. Compared with traditional style diesel machines, having this option opens doors for you as the owner to decide how you will power your quarry without being reliant on low fuel costs or consistent grid power.
By highlighting the differences between these machines, the benefits become clear, the initial cost may be higher, but the expense is quickly negated by the 30% difference in production cost.
Not only does electric technology bring down running and thus production costs, but it also adds environmentally friendly credentials to a business, with more projects and initiatives calling for some type of ‘green’ compliance, these machines can aid not only winning these contracts but owning this growing space.
With Keestracks E-Machines leading the full electric field, sacrificing efficiency and production viability for an improved carbon footprint is no longer a concern. As the saying goes “you can’t have your cake and eat it too” with these you can.